The pharmaceutical industry depends on cold storage to protect vital medicines from contamination, mishaps and degradation. Cold chain logistics require warehouses that are GMP compliant and offer specific environmental conditions for temperature-sensitive products.
To ensure constant temperature and to avoid product degradation, the warehouses must be equipped with sophisticated monitoring equipment and systems. Regulatory compliance is also critical for maintaining the quality of a pharmaceutical product.
Temperature-controlled storage
To ensure the efficacy of vaccines, antibiotics and other medications They must be stored at a temperature that is cold. Exposure to extreme temperatures can result in their potency being diminished and be rendered ineffective, which could result in severe health problems for patients. Furthermore, inadequate storage may cause substantial financial losses for pharmaceutical companies because of product loss and recalls.
Temperature-controlled storage is a key component of the pharmaceutical supply chain, which must be strictly adhered to throughout the entire process. Cold chain distribution warehouses are temperature-controlled spaces equipped with state-of-the-art control and monitoring equipment to provide specific environmental conditions for cold-chain storage and transportation of pharmaceutical products. These warehouses are equipped with insulation panels as well as phase-change materials to maintain the desired temperature and safeguard the pharmaceuticals from denature.
Cold storage not only helps preserve the effectiveness of drugs however, it also shields the formulations from contamination by fungi and bacteria. These microbes thrive in humid and warm environments, and can contaminate drug formulations. This problem can be prevented by keeping pharmaceuticals separate from other products, checking their expiration dates frequently and keeping them in a designated storage area.
Pharmaceutical cold storage needs reliable industrial refrigeration systems to maintain precise temperatures throughout the entire duration of the transportation cycle. Hillphoenix offers CO2 and alternative refrigerant solutions to meet these critical needs. The company’s innovative storage technology has enabled it to become an industry leader in the area of pharmaceutical refrigeration.
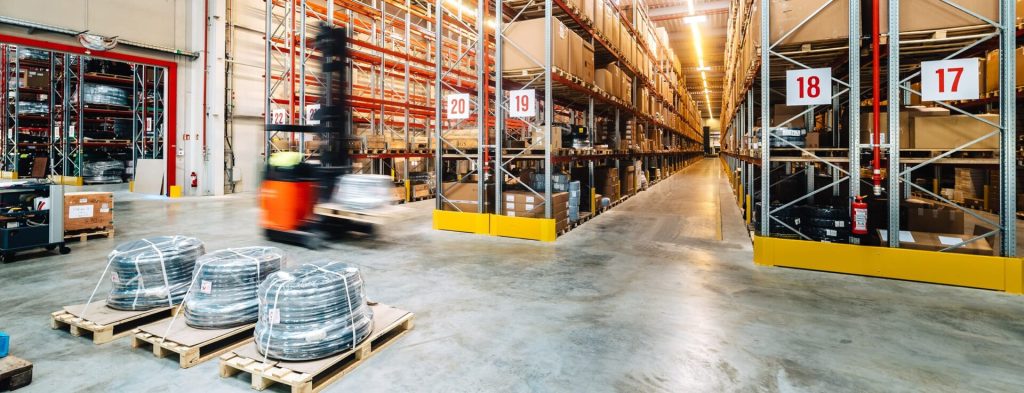
Automated storage
Pharmaceuticals require extremely optimized storage systems that ensure product integrity. Variations in humidity and temperature can have an adverse effect on the effectiveness of other medicines and vaccines. SSI SCHAEFER’s automated storage solution, Modula Climate Control, provides temperature-controlled environments for pharmaceutical operations. This vertical lift module (VLM) regulates the circulation of air in tight spaces and keeps the air temperature below freezing, which prevents ice crystals from developing. It also regulates humidity levels, ensuring that they remain lower than 5percent.
Warehouse automation has many advantages over conventional kho lanh bao quan nong san methods. For instance, ASRS systems allow for better utilization of space, which reduces the requirement for costly expansions to freezers. It also allows for greater space to store inventory, and boosts efficiency across the supply chain. Moreover, AS/RS technologies enable pharmaceutical companies to automate ultra-cold storage processes which is an important step towards Pharma 4.0.
Pharmaceutical warehouses are faced with special challenges, which include specialized storage requirements, stringent compliance with regulations, as well as security measures. They also need to handle a variety of different medications and transport them to healthcare facilities, pharmacies and retail outlets. Automated storage is crucial for these warehouses because it ensures that products remain safe and effective. AutoStore is an industry-leading warehouse automation solution specifically designed for the pharmaceutical industry. The patented Cube Storage Technology maximizes the use of space, allowing more storage to be stored in less space. Robots float above the Grid to locate and deliver items to order pick and replenishment, saving time and cutting down on the cost of labor.
Compliance with the requirements of regulatory agencies
Pharmaceutical companies must abide by strict regulatory standards to ensure the safety of their product. This includes ensuring that vaccines, medicines, and other temperature-sensitive medications are stored in the correct conditions. This is critical to preventing denaturation, which can result in a decrease in effectiveness or even compromise the quality of the product.
Temperature monitoring systems as well as detailed documents are required to ensure regulatory compliance. The systems have to be tested and validated to ensure accuracy and dependability. They should also be able track the progress and condition of a product’s manufacturing to distribution. The systems must also be able detect mistakes and deviations and alert the stakeholders.
This is especially important for vaccines that are crucial tools in combating and preventing disease. Vaccines should be stored at the correct temperature to remain effective. Deviations from the recommended temperatures can render vaccines useless. Infractions to regulations could result in high-cost fines or a reputational affront.
Fortunately, advances in technology and collaborative efforts among stakeholders have helped to improve the integrity and safety of temperature-sensitive medications. Robotic systems, for example, can simplify inventory management and reduce errors. They can also help to improve warehouse operations and decrease energy consumption. Pharma companies that must adhere to strict sustainability standards will reap the most benefits from this.
Temperature-sensitive medications
A lot of pharmaceuticals require special handling and storage conditions due to their temperature sensitivity. They could be uneffective or even dangerous when exposed to high temperatures. For instance, a dose of diazepam when exposed to extreme temperatures may be reduced by 25% in power. The good news is that most of these medications indicate recommended storage guidelines on their packaging or in the full prescribing instructions that accompany the medication. The temperature range for medications that are sensitive to heat can be temporarily “extended” when stored at an alternative temperature. However, the suggested storage guidelines must be followed.
Vaccines are especially sensitive to temperature fluctuations and deviations from the recommended storage conditions could render them useless. This is a significant threat to the public health since vaccines are essential to fight disease and transmission.
Cold storage is crucial for pharmaceutical manufacturers, pharmacies and wholesalers in order to maintain the integrity of pharmaceutical products. Use of reliable refrigeration units ensures compliance with the strictest regulatory requirements and assures the efficacy and quality of pharmaceuticals. They not only make sure that temperatures are within acceptable boundaries, but they also monitor and record information in real-time. This enables temperature-controlled transportation, and can help identify potential issues. They can also be programmed to send an alert if the temperature in the unit falls below the specified temperature.